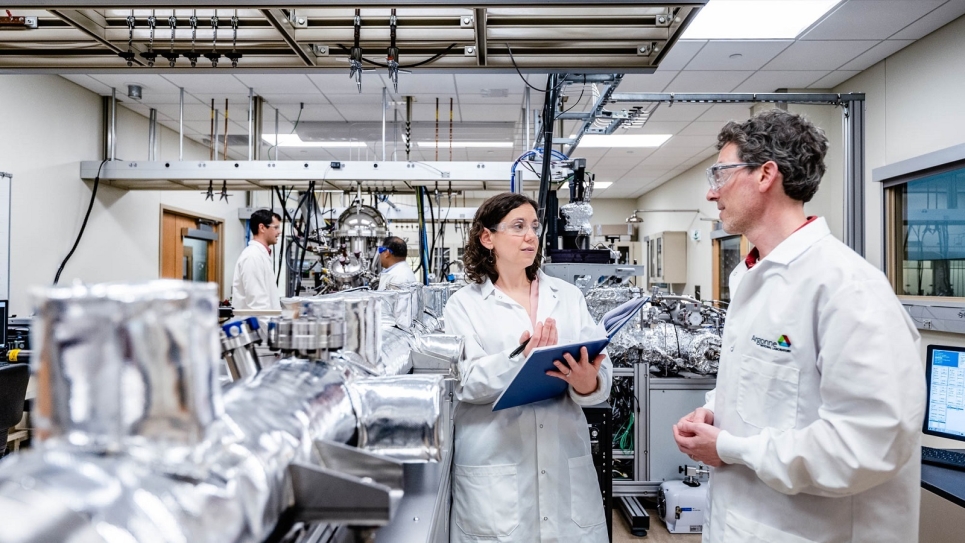
Electrochemical Discovery Laboratory at Argonne. Far right: director Brian Ingram; left to right: deputy directors Justin Connell, Rajeev Surendran Assary and Krista Hawthorne. (Image by Argonne National Laboratory.)
C-STEEL to develop cost-effective method for decarbonized manufacturing for steelmaking without a blast furnace.
Steel has a major impact on everyone’s lives and our economy. It is crucial to cars, trucks, airplanes, buildings and more. However, there is a significant issue with its production process. Globally, it accounts for a large percentage of greenhouse gas emissions from the industrial sector.
The U.S. Department of Energy (DOE) recently announced $19 million in funding over four years for DOE’s Argonne National Laboratory to lead the multi-institutional Center for Steel Electrification by Electrosynthesis (C-STEEL). The center’s charge is to develop an innovative and low-cost process that would replace blast furnaces in steelmaking and reduce greenhouse gas emissions by 85%.
“It’s a big target that has a high reward if successful,” said Brian Ingram, the C-STEEL director and an Argonne group leader and materials scientist.
C-STEEL is a key project of the DOE’s Industrial Heat Energy Earthshot initiative, which aims to significantly cut emissions from the energy-intensive process of industrial heating. Partners in the center include Oak Ridge National Laboratory, Case Western Reserve University, Northern Illinois University, Purdue University Northwest and the University of Illinois Chicago.
The most energy-intensive step in steel production involves converting iron ore into purified iron metal or iron alloys using blast furnaces. This demands temperatures of 2500 to 2700 degrees Fahrenheit, hotter than an erupting volcano. The center’s target is to develop a process that will essentially eliminate that heat demand, achieving an 85% reduction in greenhouse gas emissions by 2035.
“While current steelmaking requires intense heat from blast furnaces, our electrodeposition process will need low or even no heat input at all,” Ingram said. “It will also be cost efficient and adaptable to industrial-scale operations.”
The electrodeposition process involves dissolving iron ore in a solution and using electricity to initiate a reaction that deposits a useable iron metal or alloy for steelmaking. The solution is a liquid electrolyte similar to those found in batteries.
“We will be building upon the immense knowledge base we gained about different battery electrolytes from the work done by the Joint Center for Energy Storage Research, led by Argonne,” Ingram said.
The project has three thrusts. Two of them will investigate different processes for electrodeposition. One process will operate at room temperature using water-based electrolytes. The other will use a salt-based electrolyte and will function at temperatures 1800 to 2000 degrees Fahrenheit below current blast furnaces. The energy for this process is low enough that it could be provided by renewables or waste heat from a nuclear reactor.
A third thrust will focus on gaining an atomic-level understanding of each process. The goal of this thrust is to exert precise control over both the structure and composition of the metal products so that they can be incorporated into existing downstream processes of steelmaking.
Each thrust will incorporate an artificial intelligence-based platform to ensure a unified approach to electrolyte design. To that end, C-STEEL will be drawing upon the world-class computational resources of two Leadership Computing Facilities, one at Argonne and the other at Oak Ridge. Both are DOE Office of Science user facilities.
C-STEEL will also take advantage of the materials characterization capabilities of two other DOE user facilities at Argonne, the Advanced Photon Source and the Center for Nanoscale Materials.
“Another key part of the center is that one of the partner universities is a minority-serving institution, the University of Illinois Chicago,” said Ingram. “Through their participation and other actions, we will be forming a diverse team to contribute to our research efforts.” C-STEEL also plans to implement outreach initiatives, mentorship programs and career development opportunities for students and postdocs to excite the next generation of scientists.
This research is being funded by the DOE’s Office of Science, Basic Energy Sciences and Advanced Scientific Computing Research.
==========
The Argonne Leadership Computing Facility provides supercomputing capabilities to the scientific and engineering community to advance fundamental discovery and understanding in a broad range of disciplines. Supported by the U.S. Department of Energy’s (DOE’s) Office of Science, Advanced Scientific Computing Research (ASCR) program, the ALCF is one of two DOE Leadership Computing Facilities in the nation dedicated to open science.
Argonne National Laboratory seeks solutions to pressing national problems in science and technology. The nation’s first national laboratory, Argonne conducts leading-edge basic and applied scientific research in virtually every scientific discipline. Argonne researchers work closely with researchers from hundreds of companies, universities, and federal, state and municipal agencies to help them solve their specific problems, advance America’s scientific leadership and prepare the nation for a better future. With employees from more than 60 nations, Argonne is managed by UChicago Argonne, LLC for the U.S. Department of Energy’s Office of Science.
The U.S. Department of Energy’s Office of Science is the single largest supporter of basic research in the physical sciences in the United States and is working to address some of the most pressing challenges of our time. For more information, visit https://energy.gov/science.